Whole Foods Employees Feel They’re Being Punished Through New Inventory System
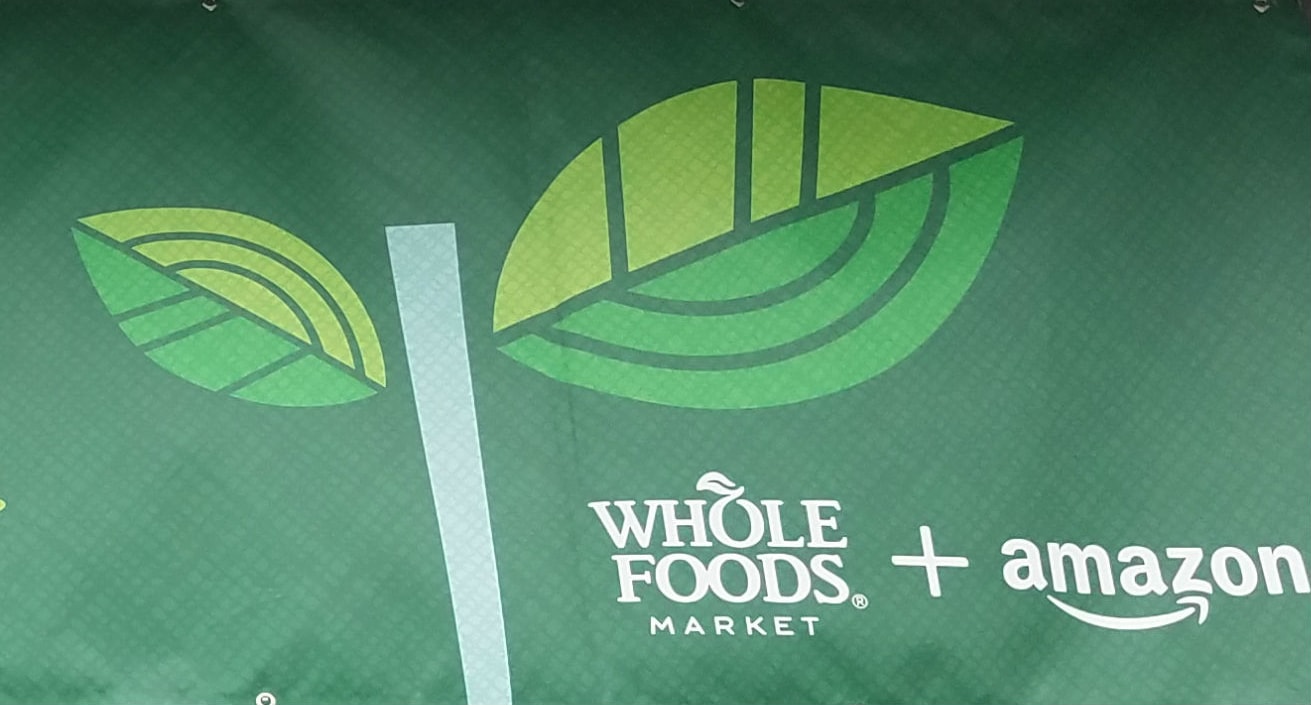
Whole Foods has been implementing a new inventory management system recently, but it’s come at a steep price for many of its now stressed-out employees.
A report from Business Insider interviewed 27 employees of the grocery chain, some of whom had recently left their jobs there. They described the new system, called OTS (Order-to-Shelf), as stressful, punitive, and morale-depleting.
One Whole Foods employee, who spoke to Foodbeast on the condition of anonymity, described the new inventory system as follows:
“OTS pretty much holds the “a place for everything, and everything in its place” adage as its core. As much as is possible, product types are kept together, and within that there’s a tendency to try to group brands. It’s advantageous and logical for someone with a structured, detail-oriented mind set. That being said, it can sometimes be frustrating to be urged to leave a hole in a display, when there is product that could fill that empty space with minimal reshuffling.”
The program has been around roughly since the end of October, according to the employee. Staffers who spoke to Business Insider also said that on top of the organizational requirements, are inspection “scorecards” that are filled out at various levels of the organization. During these inspections, store aisles and storage rooms are walked through to ensure everything is in its proper place for each department. Employees are also quizzed on information like department sales goals and top-selling products. A score of 89.9 percent or lower (basically, not getting an A) can be grounds for firing.
Whole Foods managers conduct these “walks” twice a week, while regional managers come through once a month. Stores must also pass walkthroughs conducted by the executive team from Whole Foods’ Austin headquarters.
The employee who spoke with Foodbeast noted that at least one of the inspection requirements seemed overly rigid. Their department would get marked down if there were gaps in their aisles for products that had arrived, but were pending review before being stocked on shelves.
Those who talked to Business Insider cited the “walks” as a major reason for new stress amongst team members. “Seeing someone cry at work is becoming normal,” one supervisor said, with another employee stating that “the fear of chastisement, punishment, and retribution is very real and pervasive.” Whole Foods claims that the system gives their workforce more opportunities to engage with customers, a statement that several of those interviewed disagreed with.
Food shortage crisis in @WholeFoods, with empty aisles across the country! A well intended system, gone bad. “Over To The Shelf, a militaristic system crushing the morale and leading to many items being out of stock. https://t.co/ovodjwR6kS pic.twitter.com/yLVBi8DLbs
— C. S. Prakash (@AgBioWorld) January 18, 2018
Several also attributed OTS to a stocking problem that many Whole Foods locations have had of late. The inventory management system requirements can lead to food shortages in stores. This is on top of labor shortages that result from employees getting fired due to OTS scores or others leaving because they view the system as “absurd.”
While the new requirements seem to be rigid, numerous, and stressful, the employee who Foodbeast interviewed had found at least one workaround to help keep product flow going.
“[As] long as I ask if I can shift product around and swap shelf tags in and out, I’ve found that at least on my team, creativity, proactivity, and flexibility are assets rather than liabilities… perhaps it’s the other members of my team subtly thumbing their noses at OTS. We all pretty much have the attitude of “we can’t sell it if it’s not out on the floor,” so if things need to cycle in and out then so be it.”